Interested in 3D printers but don’t know which one to buy? Visit Top 3D Shop and check out our 3D printer buying guide, we’ll help you choose the machine you need!
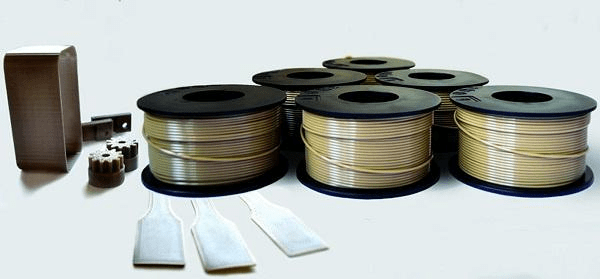
To increase the reliability of automobiles, materials must be not only durable, but also possess such qualities as chemical inertness, wear resistance and heat resistance. This combination guarantees high strength while reducing maintenance.
On the one hand, this is a big plus for buyers due to lower costs, on the other hand, it is a benefit for manufacturers receiving higher quality products through the use of parts with increased resources, which has a beneficial effect on the image.
Until now, metals have been considered the main materials, since they possess the necessary combination of the listed qualities. At the same time, metal components are overweight. Lowering the mass allows you to achieve increased fuel economy and, as a result, reduce carbon dioxide emissions. Recently, this moment is taken into account more and more often.
PEEK replaces metals
All this becomes possible when using the highly effective polymer PEEK (polyetheretherketone). Thanks to its semi-crystalline structure, PEEK can be operated at temperatures significantly higher than the glass transition temperature of 143 ° C, which makes this material an ideal choice for the automotive sector, where the parts of transmissions and engines operate most of the time at temperatures above 150 ° C. PEEK parts meet requirements with a melting point of 343 ° C and a service threshold of 260 ° C.
In addition to mechanical resistance, PEEK is also chemically inert. This is an important property for transmission parts and other components that are in direct contact with oils or fuel. By replacing metals with PEEK, it is possible to reduce the weight of individual parts by 70%, which reduces fuel consumption by 1-2%. In addition, the wear rate of PEEK parts is 25-75% lower than that of metal counterparts, and the parts are more resistant to wear with a lack of lubrication. Finally, replacing metals with PEEK reduces the noise level.
3D-printed parts from PEEK
The most effective method of manufacturing parts from PEEK is 3D printing, which allows you to create components of complex geometric shapes, unbearable for traditional production methods. More importantly, consumable savings. For example, FFF (Fused Filament Fabrication) 3D printing technology uses plastic filament that undergoes melting and layering. During the process, only the material of which the finished product will be composed is used. Compared to CNC milling, where up to 90% of the raw material is turned into chips, 3D printing can significantly reduce raw material costs.
Although FFF printing is not suitable for mass production, this method greatly facilitates the development and prototyping of finished products. However, the ability to manufacture individual components and small batches remain. The illustrations below show two 3D-printed parts (bevel gear and o-rings) made of PEEK, suitable for installation in a transmission. Both parts were printed on an Indmatec HPP 155 3D printer.
The main advantage of PEEK gears is its high resistance to mechanical stress. Rings are resistant to fuels and lubricants, which increases their survivability.
The decisive criterion in the additive production of functional automotive components remains their strength compared to parts manufactured by conventional methods. The illustration below shows a comparative analysis of the characteristics of parts made from PEEK by selective laser sintering (SLS), layer-by-layer extrusion printing (FFF) on Indmatec 3D printers and injection molding of polymer powder (PIM). It is noteworthy that with regard to the tensile strength of finished products, FFF printing shows results comparable to casting. Comparative strength testing was carried out in the horizontal plane (X / Y), since the layering of printed parts inevitably leads to a decrease in tensile strength along the Z-axis by about 30%.
In addition to the possibility of manufacturing parts of complex geometric shapes, 3D printers are able to create components with a lightweight design, as an example in the following illustration shows. Casting does not allow to produce such structures. Due to the honeycomb structure, the strength remains at the level of printed parts with full content, but the mass of the product and material consumption are significantly reduced.
3D printing in combination with high-performance polymers such as PEEK can be an alternative to the production of metal parts in the automotive industry and provide increased car efficiency coupled with the simplification of the implementation of ideas in finished goods.