Interested in improving your business with 3D technologies but don’t know where to start? Visit Top 3D Shop and check out our 3D scanner reviews!
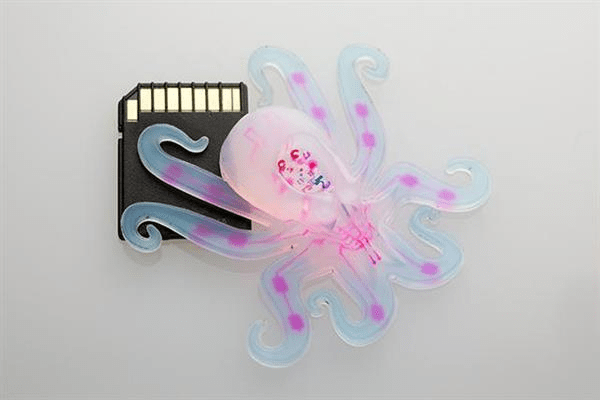
Harvard researchers have unveiled the world's first fully soft robot made with additive manufacturing.
So far, all soft robot designs have used rigid structural elements or hardware in one way or another. Harvard, on the other hand, is completely elastic, and movement is provided by chemical reactions. The robot was baptized with the "octobot", similar to the octopus, which became the inspiration for the design. The device was created by a team led by Robert Wood and Jennifer Lewis.
According to Professor Wood, the main task of the project was to prove the very possibility of completely soft robotics. “Until now, replacing hard components like batteries and electronics with similar soft systems and then assembling such devices was considered problematic. This study shows that we can easily make key components of a simple, fully flexible robot, and lays the foundation for more complex designs, ”says Wood.
The key moment was the replacement of the usual electromechanical drive with a pneumatic one, in which the pressure is generated by the reaction of hydrogen peroxide reduction. “The great thing about hydrogen peroxide is that it allows us to completely replace rigid energy sources with a simple reaction with a catalyst — in this case, platinum,” says Michael Wehner.
The creation of a robot was made possible thanks to additive technologies. “We used a hybrid assembly method: every required functional component was printed, including fuel tanks, actuators and moving parts, and it was done quickly. Octbot serves as a simple demonstrator of the use of integrated design and additive technologies to achieve autonomous functionality, ”says Professor Lewis.
The inspiration for the design is clearly the octopus, whose strength and agility never cease to amaze the developers of soft robotics. So far, the Octobot can only move its tentacles, and autonomy should be understood as its ability to independently initiate movements. It is possible that the next versions will be able to crawl, swim and pull ships into the abyss, but so far this functionality is far from. Even the current version was the result of a series of several hundred 3D-printed prototypes, which were used to refine the design of the pneumatic drive.
Movement control is carried out using a microfluidic logic circuit - an analog version of an electronic generator. A network of microvessels controls the distribution of gases obtained from hydrogen peroxide, and the supply of fuel in the internal tanks is enough for about eight minutes of operation. In the long term, the researchers hope to achieve full mobility and equip robots with flexible sensors. Rescue operations, ocean temperature measurements and even military reconnaissance are being considered as potential applications.
The most difficult moment in designing such a robot is 3D printing of the internal structure. The rest of the design is simple enough and easy to scale. “The system is easy to make with a combination of soft lithography, casting and 3D printing. We can produce such devices very quickly. This project should be considered a proof of concept. We hope that our methodology for creating soft autonomous robots will be useful to researchers in the fields of robotics, materials science and advanced manufacturing technologies, ”explains graduate student and co-author of the project, Ryan Truby.