Are you thinking of getting a 3D printer for your home or business? Visit Top 3D Shop and read our latest reviews. We will help you get the machine you need!
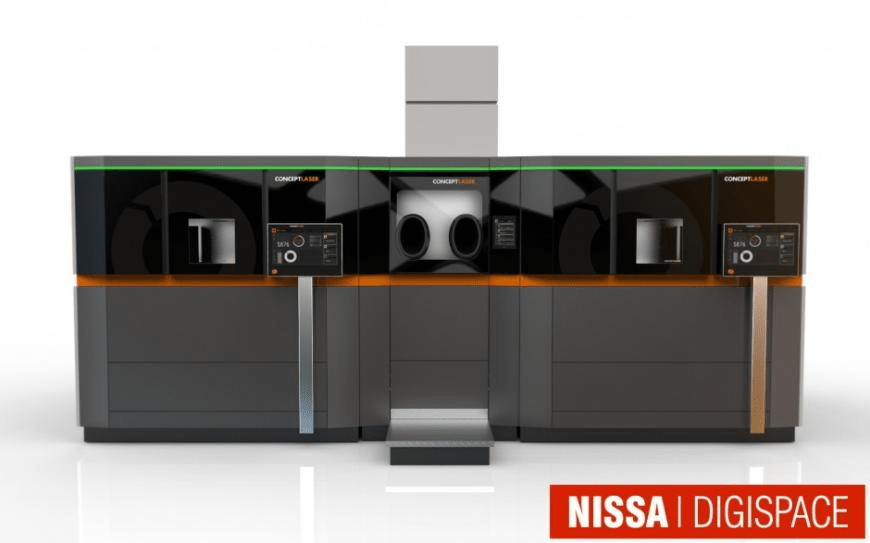
Production technologies and equipment previously presented on the market relied on the concepts of additional sources of laser radiation and increase their power, increase the speed of construction and expand the print area. The car was considered as a "stand-alone" solution - without thoughtful integration into the production process. First, the preparation of equipment for printing, then the actual printing was carried out sequentially. Offering a new equipment architecture, Concept Laser expects to add new qualitative aspects to traditionally quantitative criteria. “Essentially, we are talking about dividing additive manufacturing systems into any number of freely combinable modules for independently preparing equipment for printing / printing / processing a printed product,” explains Florian Bechmann, head of research and development at Concept Laser. - Parallel processes of loading powder and unloading finished products increase effective printing time, thereby significantly reducing the “downtime” of machines that previously operated autonomously. Here lies a huge potential for increasing the efficiency of the production chain. For industrial serial production, this fundamentally new approach, which differs sharply from the usual "quantitative" equipment concepts, means the opportunity to take another step forward. '
New concept of the Additive Factory of the Future
The emerging regional 3D printing centers are now serving as service providers for countries from around the world, gradually moving from “prototyping” to plans for the development of flexible serial production at the industrial level. Additive enterprises are under pressure from traditional suppliers: there is a need for space, an expansion of the equipment park and the range of production tasks, and optimization of terms. The new concept, proposed by Concept Laser, has examined a number of interesting solutions to these problems. Production is separated from the preparation process - “at the equipment level”. At the same time, the availability of all components increases: additive production goes to round-the-clock downloads. Automated material flow significantly reduces operator workload. Selective laser melting machines through interfaces integrate with traditional CNC machines for hybrid production, as well as with subsequent operations (post-processing / finishing).
Separation of "preparation", "production" and "post-processing"
The basis of the new production architecture is the separation of “preparation”, “production” and “post-processing”. In particular, they proposed a flexible system for loading machines, the physical separation of the processes of loading materials and platforms and their dismantling. The task set is to more precisely coordinate production components through a single interface and increase the flexibility of technological processes to form an integrated approach. This was made possible thanks to the verified modular structure of the “feed sections”, “construction and processing systems”: the combination and interaction of these modules is designed to significantly increase the flexibility and functional load of the equipment. By combining modules in a certain way, you can improve the work with the whole range of materials available today and at the same time significantly reduce production costs. In general, the level of efficiency and accessibility of the production system will increase markedly, and the need for working space will drop sharply. Emulation of production scenarios has confirmed that the occupied space can actually be reduced by 85% compared to current needs. Additional laser modules increase overall system performance, especially when 3d printing a large number of repeating or independent parts on a single printing platform. “Thanks to multi-laser technology, build speeds have grown dramatically. The size of the print area has also become significantly larger. Now, with the example of the concept of integrated equipment, we want to show how the principles of the fourth industrial revolution, Industry 4.0, are able to change the additive production, which is the industrial strategy of the future. Here lies a huge potential for improving the efficiency of enterprises and optimizing technology for the tasks of mass production, ”explains Beckmann.
New modular architecture for additive manufacturing systems - print system
On the first day of the formnext by TCT 2015 exhibition, a new printing system with a working area of 400 x 400 x> 400 mm3, equipped with four laser sources, was demonstrated at the Concept Laser booth. In addition to the varying diameter of the laser spot in the melting zone, this model has several configuration options: 1, 2, or 4 laser optical modules with a power of 400 to 1000 watts. An optional fault tolerance system ensures that if one laser fails, the other three cover the entire print area — the construction process will not be interrupted. “Additional laser sources can increase speed