Interested in 3D printers but don’t know which one to buy? If you’re looking for a worthy machine, visit Top 3D Shop and check out our 3D printer reviews, we’ll help you choose the machine you need!
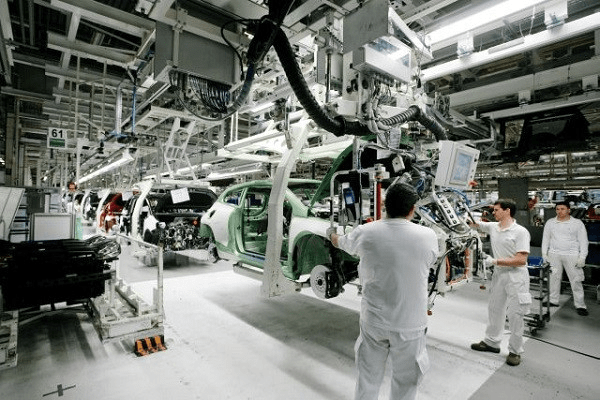
The Portuguese car factory Volkswagen Autoeuropa saves on assembly costs through additive manufacturing. No expensive industrial setup is required - Ultimaker desktop 3D printers are sufficient.
Every year, the Portuguese company rolls out about one hundred thousand cars from the shops. Although production is largely automated, assembly is mostly done by hand. Management is constantly striving to optimize the efficiency of the expensive labor force, while saving on the purchase of additional equipment.
One of the solutions was the installation of our own 3D printing farm, consisting of a set of Ultimaker FDM printers. The farm is used for the manufacture of assembly equipment - various devices that facilitate and speed up installation without compromising the quality of the products.
For example, for the installation of wheels, special protective guide templates are used, which help to quickly tighten the bolts without fear of hurrying to damage the wheel rims with a power tool. A huge number of such devices is not required, because only a few assemblers use them, and therefore ordering small batches of equipment from third-party manufacturers previously cost about € 800 apiece. Casting piece products is an expensive pleasure. Each template costs € 21 to 3D print. At the same time, the waiting times for finished products were also significantly reduced: if earlier it took almost two months from the moment of placing an order to receiving the tools, then it took only about ten days to design, 3D-modeling and 3D-printing.
“It took 25 days to manufacture the device for the labeling of logos and labels, when we ordered them externally, and the cost reached € 400. 3D printing has reduced the time to four days and the cost to € 10 apiece. The window trimmer cost € 180 a piece, but now costs only € 35, and it took six days instead of eight to create, ”says plant manager Luis Pasqua.
What is most remarkable is that having our own additive manufacturing allows you to quickly make adjustments to the design of the developed tooling, improving the design and increasing the efficiency and convenience of assemblers. In total, the plant is armed with seven inexpensive desktop 3D printers, which provide 93% of the company's needs for specialized assembly tools. Since the start of the 3D printing farm in 2014, savings in tooling development and production have been 91%, and time has been reduced by 95%. In monetary terms, the savings for 2016 amounted to about € 150 thousand, and according to the results of the current year, this figure is likely to grow one and a half to two times. The money spent on the purchase of 3D printers paid off after just two months.