Interested in improving your business with 3D technologies but don’t know where to start? Visit Top 3D Shop and check out our 3D scanner reviews!
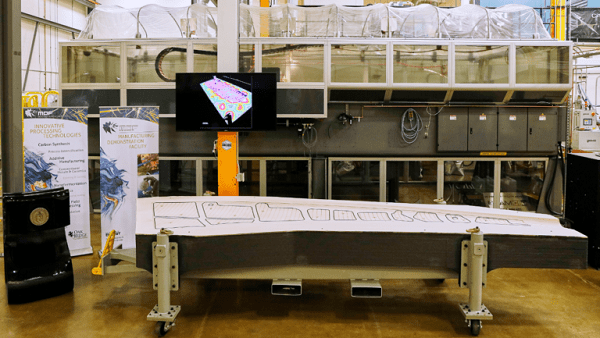
Oak Ridge National Laboratory (ORNL) and Boeing made history as the largest single piece of the 3D printed product.
According to ORNL's press service, the relatively inexpensive tooling was printed from an ABS composite with carbon fiber additives. It took about 30 hours to make the part. The dimensions of the finished product are 5.33x1.67x0.46 meters, which makes it the largest ever printed the whole object. Tooling is used as a template for cutting, and the weight of the product reaches a considerable 748 kilograms. A large-format BAAM 3D printer manufactured by Cincinnati Incorporated was used for printing. Similar systems are used by Local Motors for the production of 3D-printed car bodies.
“The existing metal tooling options we have used so far are outsourced and take up to three months to manufacture using traditional manufacturing methods,” says Leo Christodoulou, Boeing's director of procurement. “3D printed tools such as this Boeing 777X wing panel cutting tool save time and cost. This is part of our overall strategy for applying additive technologies to key manufacturing sectors. "
The celebration took place in a closed environment at the ORNL demonstration production facility. The awarding ceremony was conducted by the Guinness Book of Records judge Michael Emprick. Following the completion of testing, Boeing intends to use the new tool at the St. Louis factory while providing ORNL with operational data. The rig is designed to attach Boeing 777X composite wing skins prior to machining. Production of the updated airliner will begin next year, with the first deliveries scheduled for 2020.
“Recognition from the Guinness Book of World Records will help draw attention to our research in the field of large format additive manufacturing using composites,” said Vlastimil Kunz, head of the ORNL polymer development team. “Through 3D printing, we were able to create a tool with reduced material consumption without compromising the functionality of the finished product.”