Interested in 3D printers but don’t know which one to buy? If you’re looking for a worthy machine, visit Top 3D Shop and check out our 3D printer reviews, we’ll help you choose the machine you need!
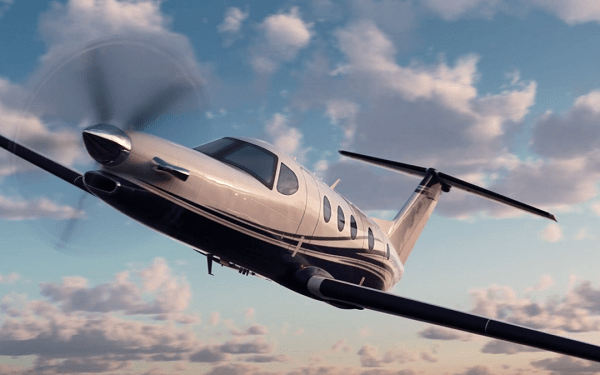
General Electric Corp. has shared details of the development of the latest ATP (Advanced Turboprop) turboprop, using a range of 3D printed components.
The first recipient of the new engines is to be the Cessna Denali business jet developed by Textron Aviation. Serial production of engines is planned to be established at a new plant in Prague, whose construction, in agreement with the Czech government, should be completed in 2022. Prototypes will be tested here, and then a number of parts will be produced and assembled. The 3D printed components are slated to be manufactured at GE's Avio Aero factory in Brindisi, Italy. Developers from Germany and Poland are also involved in the "fully European" project of the American corporation.
The first version of the ATP turboprop will develop an output of 1,300 hp. and consume less fuel than traditional counterparts. Through the use of additive technologies, the number of individual components will be reduced by about a third, contributing to higher reliability and efficiency: manufacturing complex parts instead of assemblies will help eliminate weak links, i.e. fasteners and welds, and at the same time reduce the weight of power plants. Due to this, increased comfort will be achieved: the saved weight will be used to increase the size of the cabin without reducing the range, speed or practical ceiling. Subsequent ATP models will have between 1,000 and 1,600 hp.
Next year, the Brindisi factory will receive new additive equipment, including industrial 3D printers from Germany's Concept Laser and Sweden's Arcam AB, which were acquired by the American corporation late last year. The new facilities will be commissioned in 2019. In total, Avio Aero plans to produce thirteen varieties of metal 3D-printed components, including gearboxes, heat exchangers and combustion chambers. New high-strength, heat-resistant alloys, unsuitable for use in traditional aircraft construction, will be used as consumables for 3D printing.
“We're not just replacing some production methods with others. We are reinventing design processes in the aircraft engine industry. This includes the use of new alloys, as additive technologies allow in some cases to avoid compromises. For example, we now have additive solutions for certain materials that can simultaneously reduce weight and increase production efficiency without sacrificing one factor in favor of another, ”explain Luca Bedon and Giorgio Abrate, engineers at Avio Aero.
Bench tests of ATP 3D-printed turboprop engines are due later this year, with flight tests starting in 2018. In the meantime, 3D-printed components are already being used in production of the next generation GE LEAP turbojet engines. At the international aerospace show in Le Bourget, the corporation received orders for 1,658 of these power plants for the Airbus A320neo, Boeing 737 MAX and COMAC C919 airliners.